End mills for composite materials
740
Left / right helix end mill

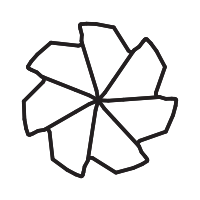
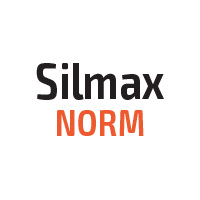
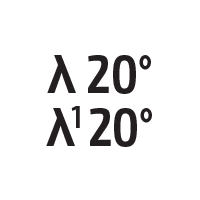
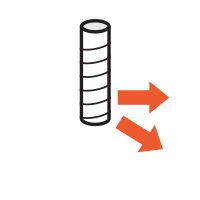
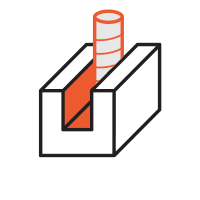
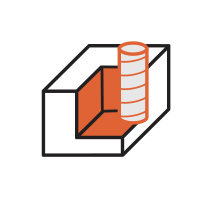
750
Multi-flute end mill

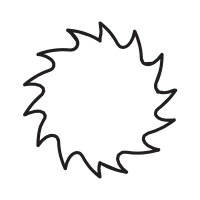
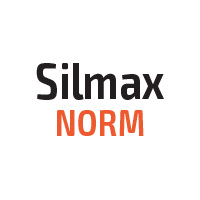
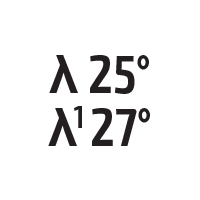
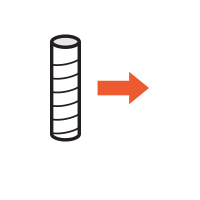
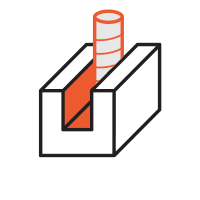
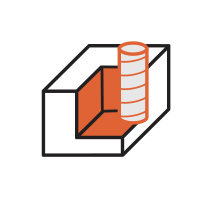
751
Multi-flute end mill with spot-facing end

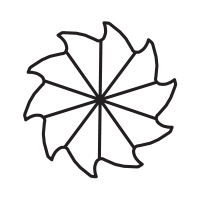
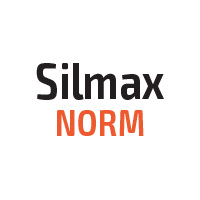
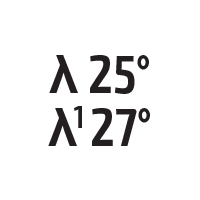
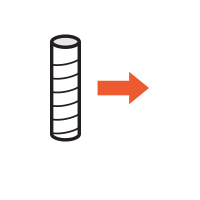
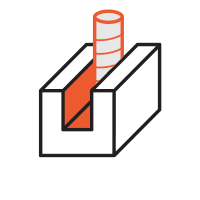
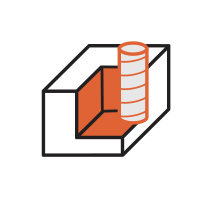
752
Multi-flute end mill with drilling end

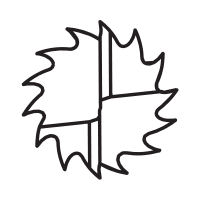
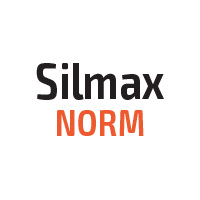
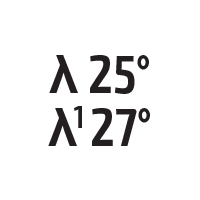
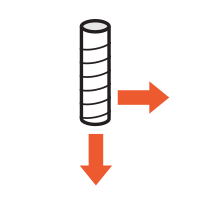
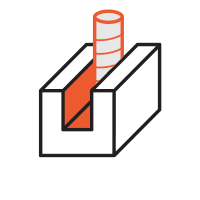
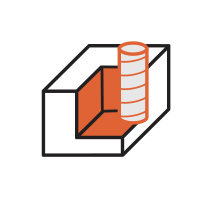
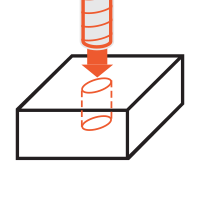
760
End mill with continuous cutting geometry

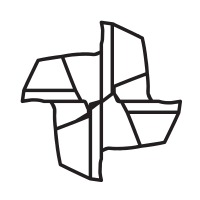
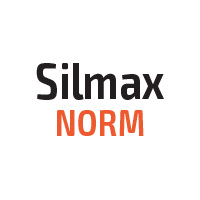
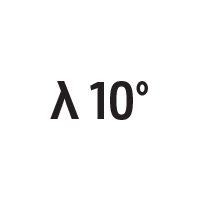
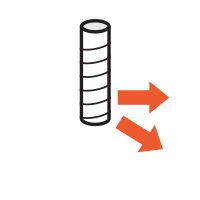
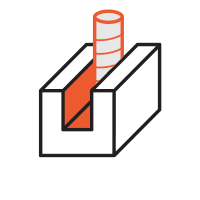
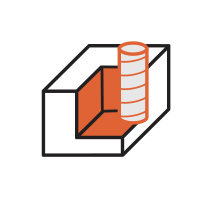
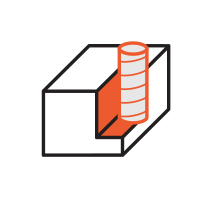
770
End mill with combined cutting edge geometry

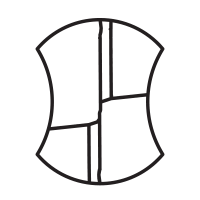
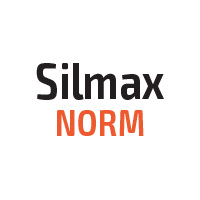
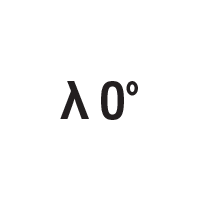
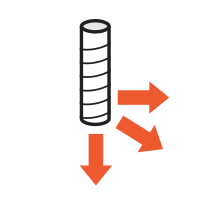
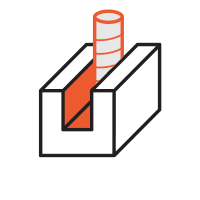
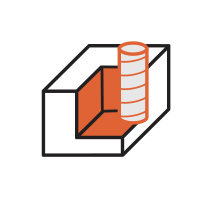
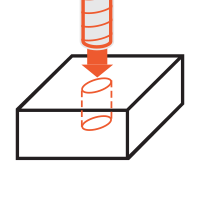
780
Front geometry drill


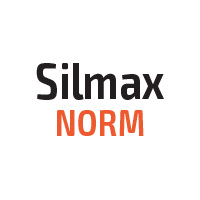
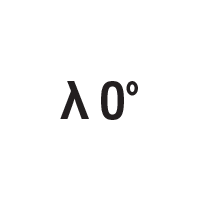
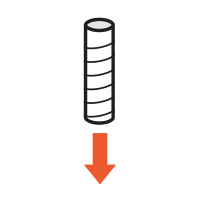
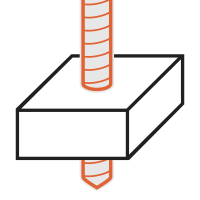

Multi-flute end mill

Multi-flute end mill with spot-facing end

Front geometry drill

Front geometry drill

Left / right helix end mill

Multi-flute end mill with spot-facing end

Multi-flute end mill with drilling end

End mill with combined cutting edge geometry

Multi-flute end mill with drilling end

Multi-flute end mill with drilling end

Left / right helix end mill

Multi-flute end mill with drilling end
End mills for composite materials: CFRP, GFRP, AFRP
The end mills for composite materials need a specific, dedicated design creating peculiar cutting geometries, Composite materials (CFRP, GFRP, AFRP, sandwich, honeycomb materials) are increasingly used in different sectors: aeronautics, automotive, shipbuilding, race components, industrial machinery (packaging, paper, robotics, food, pharmaceuticals) o in particular industrial applications.
The machining of thin-wall panels requires specific technological challenges, for which dedicated tools have been developed.
- The cross-cutting geometry creates cutting forces directed inside the panel, thus avoiding the phenomenon of delamination.
- The low-helix, continuous-cutting geometry has been developed for contour milling and pocket milling.
- The innovative combined-cutting geometry is specifically studied for machining AFRP materials (Kevlar) and honeycomb structures, thus eliminating the phenomenon of inadequately cut fibers.
Milling composite materials
The tool range for milling composite materials includes, besides standard products, a large number of special tools to meet the customisation requirements of a varied and rapidly developing market.
Drilling is one of the most widely used machining in composite-material structures. The tendency to peel-up and push-down delamination represents one of the most common problems. The variety of materials and machining methods, (manual, semi-automatic, assisted, CNC-machine drilling) makes it difficult to create a standard range.
Silmax has a wide experience in drilling composite-material structures and panels in different fields. This experience is at its customers’ disposal by a wide selection of drilling tools, which is customised according to specific applications.
CVD coating
The Diamond coating is characterised by incomparable hardness, chemical inertness, thermal conductivity, which make it the ideal choice to machine highly-abrasive composite materials.