Gun drills and accessories
5001
Single-lip drill with brazed drill head for machining centres

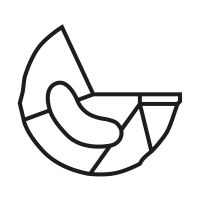
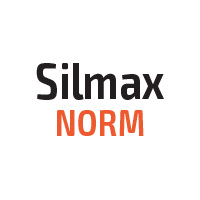
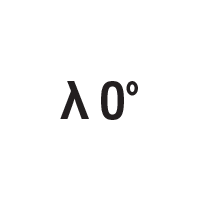
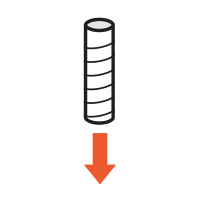
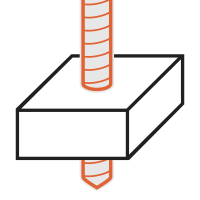
5002
Single-lip drill with brazed drill head for drilling machines

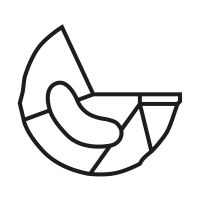
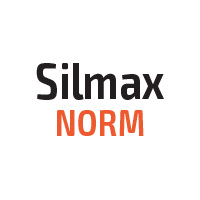
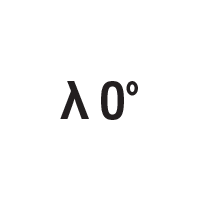
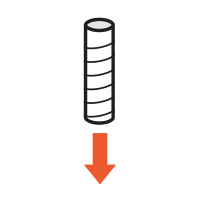
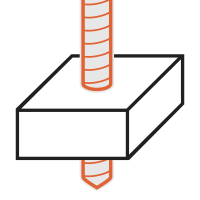
5003
Single-lip drill with long brazed drill head for drilling machnes

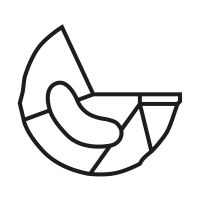
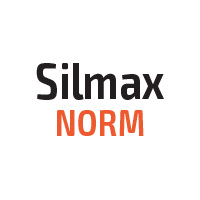
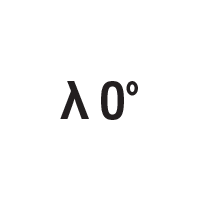
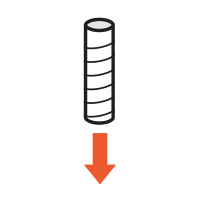
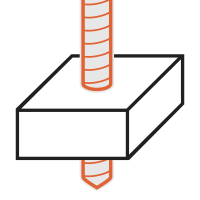
5200
Rubber anti-vibrant drilling bushes D20

5201
Reinforced rubber anti-vibrant drilling bushes D20

5300
Rubber anti-vibrant drilling bushes D30

5301
Reinforced rubber anti-vibrant drilling bushes D30

5450
Rubber anti-vibrant drilling bushes D45

5451
Reinforced rubber anti-vibrant drilling bushes D45

5520
Vulkollan sealing disc D20

5532
Vulkollan sealing disc D32

5540
Vulkollan sealing disc D40

5590
Vulkollan sealing disc D90


Single-lip drill with brazed drill head for machining centres
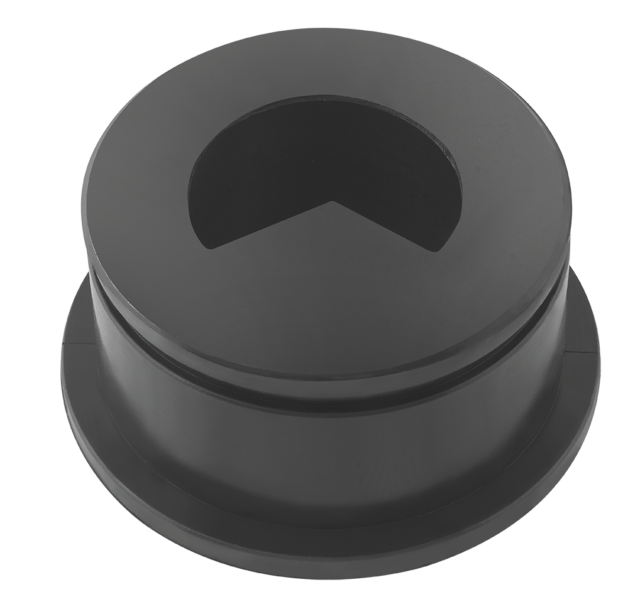
Rubber anti-vibrant drilling bushes D20
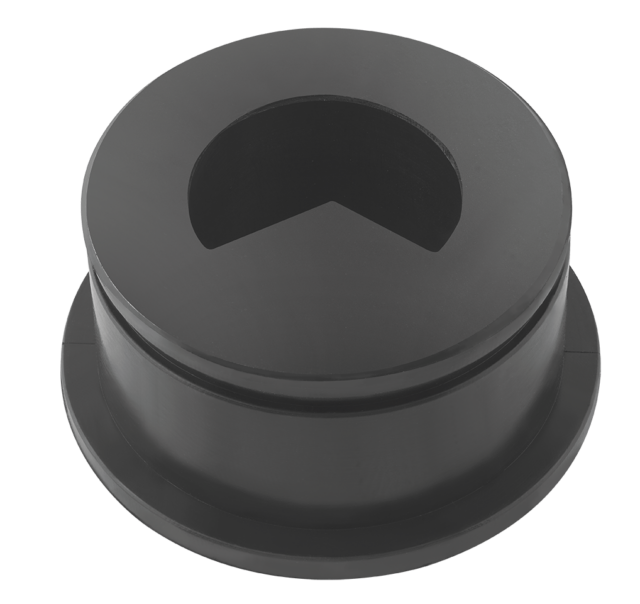
Rubber anti-vibrant drilling bushes D45

Single-lip drill with brazed drill head for machining centres

Single-lip drill with brazed drill head for machining centres
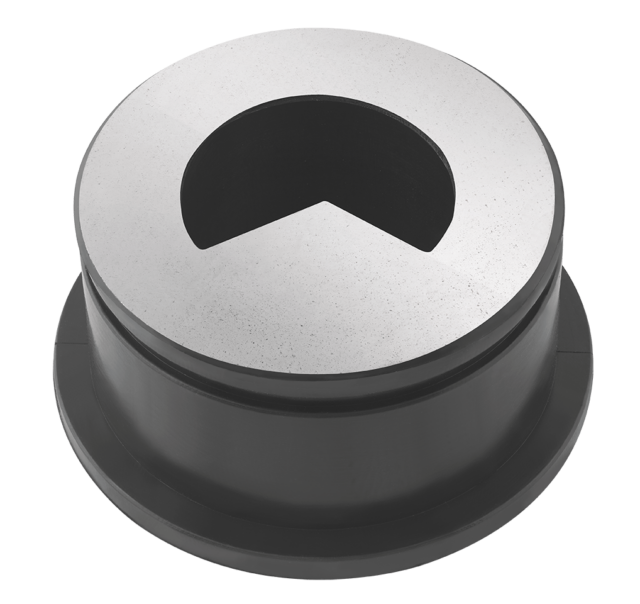
Reinforced rubber anti-vibrant drilling bushes D20
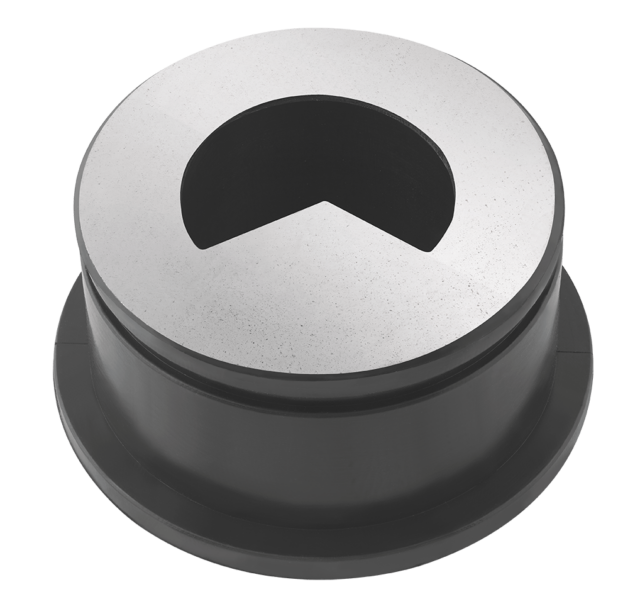
Reinforced rubber anti-vibrant drilling bushes D30
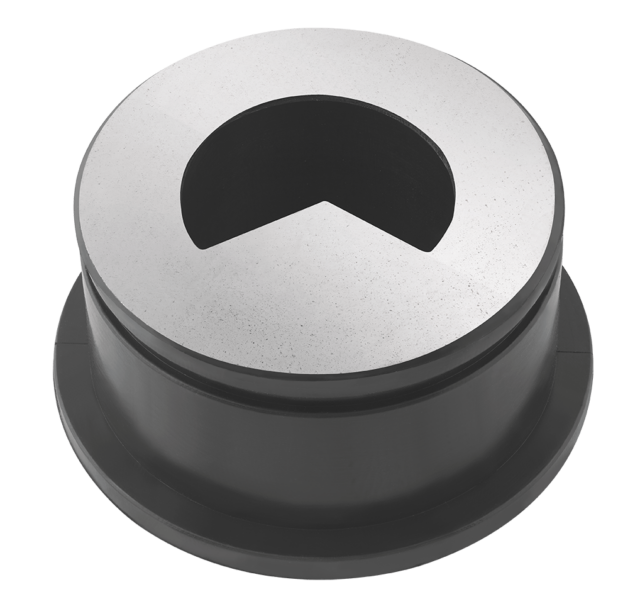
Reinforced rubber anti-vibrant drilling bushes D30

Single-lip drill with brazed drill head for machining centres
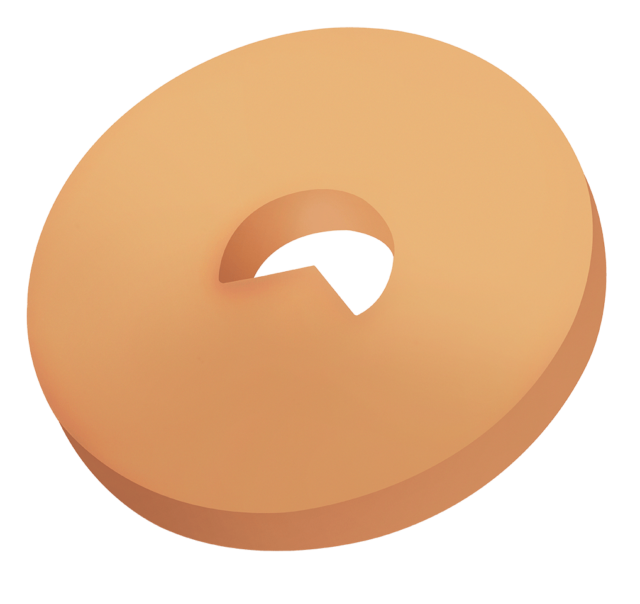
Vulkollan sealing disc D32
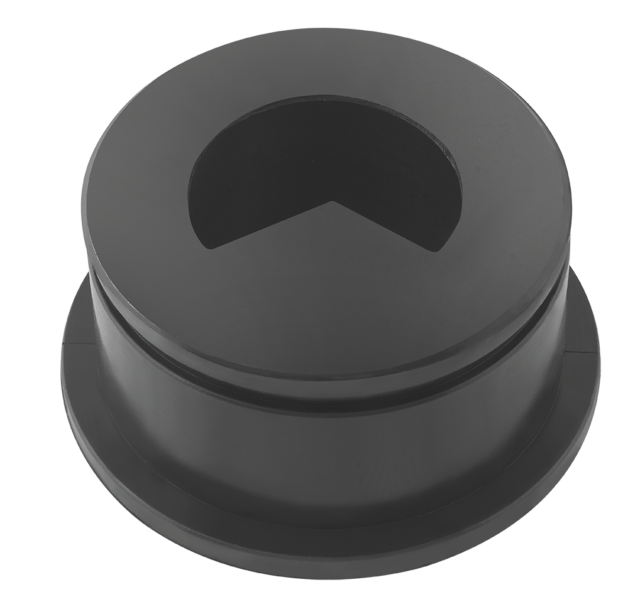
Rubber anti-vibrant drilling bushes D20
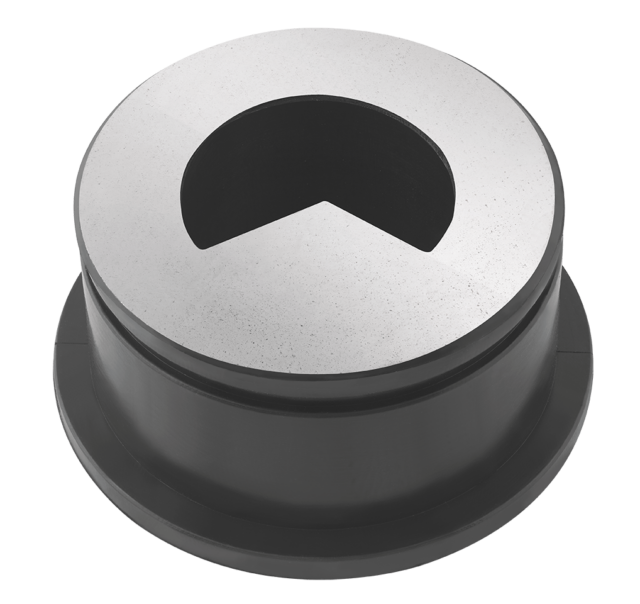
Reinforced rubber anti-vibrant drilling bushes D20
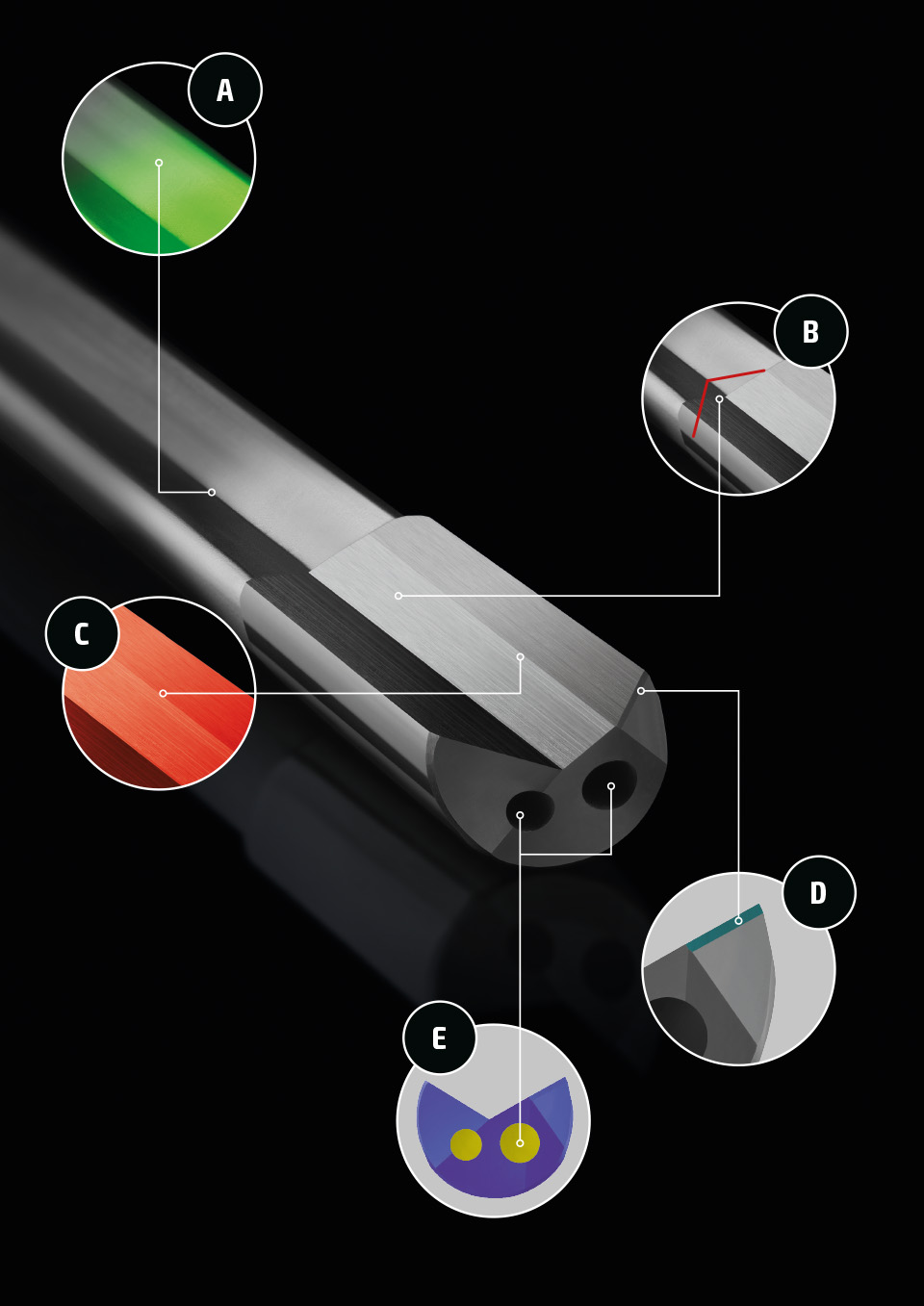
Highlights
A. High-quality hardened and tempered steel tube
B. V-shaped head seat
C. Micrograin k15 substrate optimal for a large variety of materials
D. Double hole for coolant starting from diameter 8
E. Reinforced cutting edge
Special gun drills

Solid-carbide, single-flute gun drills
The tool is made of a single lump of metal, composed of a small carbide cylinder that can be matched with a brazed steel clamping sleeve in the final part of the tool. This solution ensures particularly safe and efficient processes, as well as a longer tool life, thanks to the reduced torsional oscillations.
- Diameter range: 0.7 — 12.0 mm with 1/1000 mm increases
- Maximum length: 600 mm
- Tool usable length 80 — 100 x D

Single-flute gun drills with brazed drill head
It is the most commonly used solution in the market, developed with more elements brazed together. The tool is composed of a carbide drill head, a body (shank) and a clamping sleeve made of hardened and tempered steel. It is a very versatile type of tool, as it enables an endless number of customised versions in terms of diameters, lengths and clamping sleeves.
- Diameter range: 1.9 — 50.0 mm with 1/1000 mm increases
- Length up to 6000 mm
- Usable tool length: 40 — 50 x D
Our services
In addition to standard solutions, Silmax can also develop special solutions to meet your requirements, in consideration of the material to be machined and the particular drilling conditions. These solutions include the creation of specific geometries, step drills or reaming tools, with possibility of combining them with one of the numerous coatings we make in-house. All tools can be coated in-house by Silmax.
Silfast Service
Silmax offers its customers the possibility to have special tools with fast delivery time, 7 days from order receipt, for single-flute, brazed drills, with standard drill head and without coating.
- Available diameters
2.5 — 13.5 in 0.1mm steps. - Maximum length
1500 mm including clamping sleeve. - Typology of clamping sleeve
Download table. - Quantity
Up to a maximum of 5 pieces for each single diameter required.
The service entails an extra charge compared to products with standard delivery time. For all other diameters that are not included in this range, delivery times are standard.
Accessories

5.0 Anti-vibration drilling bushes standard version

5.1 Anti-vibration drilling bushes reinforced version

Vulkollan sealing discs
Technical information
Cooling lubricants
Guidelines for an appropriate choice of the products to be used and their optimal values of use.
A cooling lubricant is one of the most important elements in the use of gun drills: an accurate choice and a correct management can bring considerable advantages in terms of tool yield and performance.
The application of a well-performing filtration system is also recommended, as it is also fundamental for an optimal management of the whole process of deep-hole drilling.
Required conditions
Conditions required for an optimal drilling: neat oil or emulsified water with a concentration of 10-12%. In both cases, it is preferable to use products with specific additives for deep-hole drilling.

HM drills
Viscosity
7 — 10 mm2/s (Ø 0,8 — 2,0)
10 — 12 mm2/s (Ø 2,0 — 12,0)
Filter efficiency
5 — 10 μm

Brazed drills
Viscosity
10 — 20 mm2/s
Filter efficiency
10 — 20 μm
Surface finish
Thanks to its peculiar geometry, a gun drill enables to achieve a very high quality with regard to surface finish of the hole. This outcome can further be improved by using specific construction geometries. The table shows values that can be obtained by using a tool with a standard geometry.
Tolerance | Twist drilling | Reaming | Broaching | Honing | Deep hole drilling | Arithmetical mean |
---|---|---|---|---|---|---|
μm | ||||||
N12 | — | — | — | — | — | 50,000 |
N11 | — | — | — | — | — | 25,000 |
N10 | ● | — | — | — | — | 12,500 |
N9 | ● | — | — | — | — | 6,300 |
N8 | ● | ● | ● | — | — | 3,200 |
N7 | — | ● | ● | ● | — | 1,600 |
N6 | — | ● | ● | ● | ● | 0,800 |
N5 | — | ● | ● | ● | ● | 0,400 |
N4 | — | ● | — | ● | ● | 0,200 |
N3 | — | — | — | ● | ● | 0,100 |
N2 | — | — | — | ● | — | 0,050 |
N1 | — | — | — | — | — | 0,025 |
Hole runout
Approximate runout values under deep-hole drilling conditions on machines with drill bush.
Working parameters for brazed gun drill
Working parameters for carbide gun drills
1. Cast iron
Vc=80 m/min
2. Light alloys
Vc=120 m/min
3. Aluminium
Vc=130 m/min
4. Steel <800N/mm²
Vc=85 m/min
5. Ferritic / Martensitic steel
Vc=55 m/min
6. Austenitic steel
Vc=45 m/min
7. Steel <1300N/mm²
Vc=70 m/min
8. Titanium
Vc=40 m/min
9. Austenitic steel
Vc=40 m/min
Drilling with pilot drill
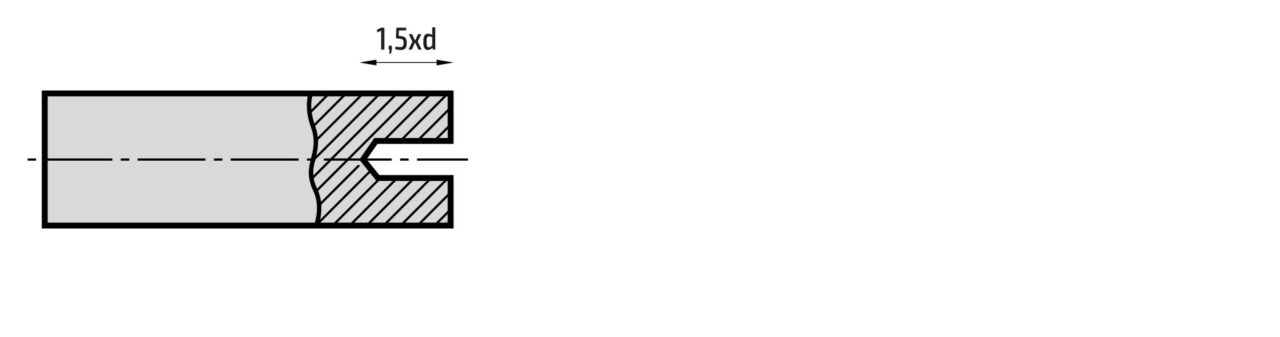
1. Execution of pilot holes
We recommend the use of Silmax carbide drills Art. 3031A. Depth required for pilot hole: 1.5 x D.
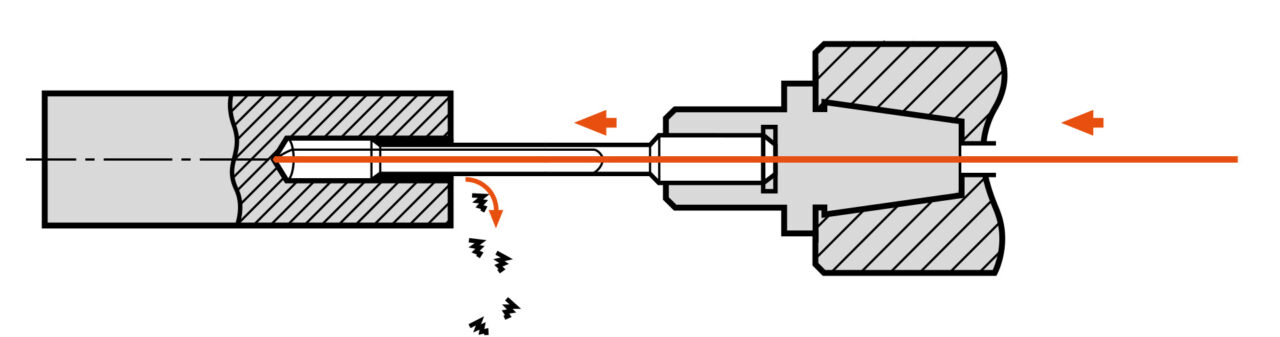
2. Entry into pilot holes and drilling cycle
Enter with gun drill on spindle rotating in the counter-clockwise direction at a maximum of 100 rpm and F 1000mm/min. Set up at +5mm from the end of pilot hole and start coolant. Reverse the direction of rotation and execute drilling cycle according to working parameters.
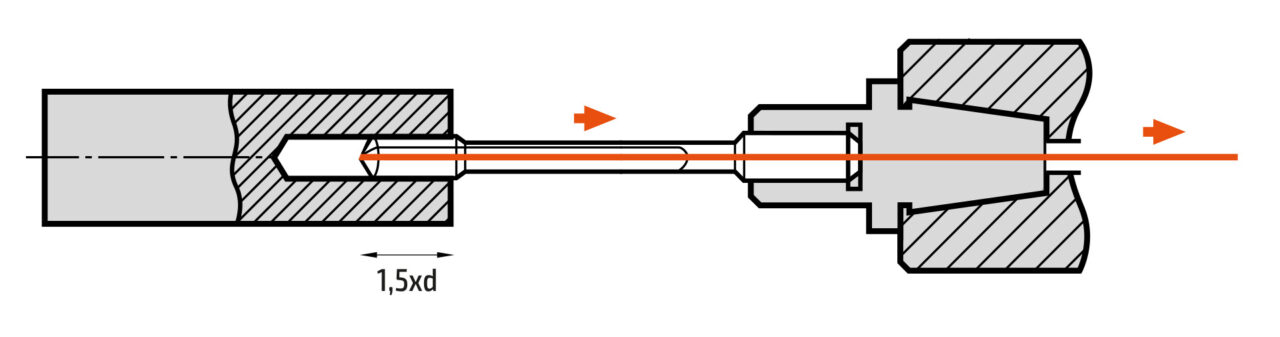
3. Exit from hole
At the end of the cycle, move tool back to the starting point at F5000 mm/min, reverse rotation and exit at 100 rpm and F1000 mm/min.
Cutting-edge geometry
La geometria standard Silmax è stata appositamente studiata per permettere di forare un ampio spettro di materiali con risultati ottimali. Tuttavia nelle situazioni particolari come per esempio materiali a truciolo lungo o difficilmente truciolabili, siamo in grado di realizzare soluzioni specifiche di geometria intervenendo su forma e affilatura oppure con eventuale creazione del romitruciolo sul filo tagliente. Nelle fasi di riaffilatura dell’utensile si consiglia di rispettare le indicazioni riportate nelle tabelle presenti. Un utensile accuratamente affilato sarà sempre al massimo delle prestazioni.
Standard grind section for single-lip drills up to 5 mm
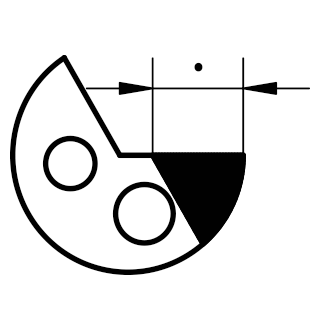
Step 1
Axis A: 40°
Axis B: +25°
Axis C: +12°
Meas.: > D/4
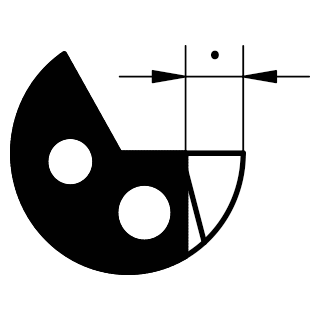
Step 2
Axis A: 30°
Axis B: +20°
Axis C: -7°
Meas.: D/4
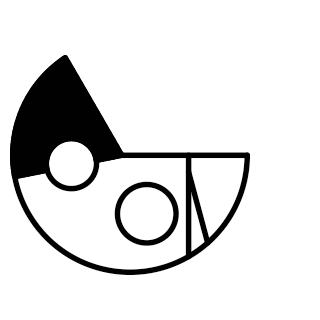
Step 3
Axis A: 35°
Axis B: +20°
Axis C: +55°
Meas.: —
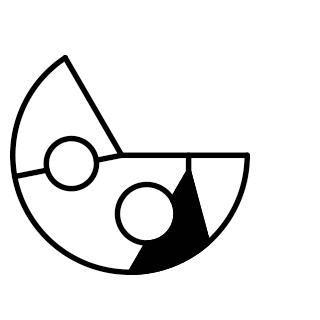
Step 4
Axis A: 0°
Axis B: +38°
Axis C: 0°
Meas.: —
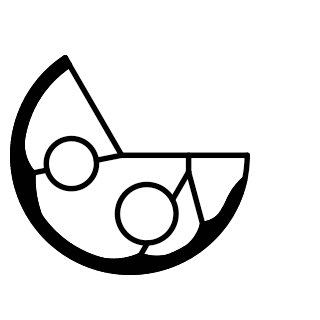
Step 5
Twist the single-lip drill lightly around the circumference
without damaging the guide chamfer.
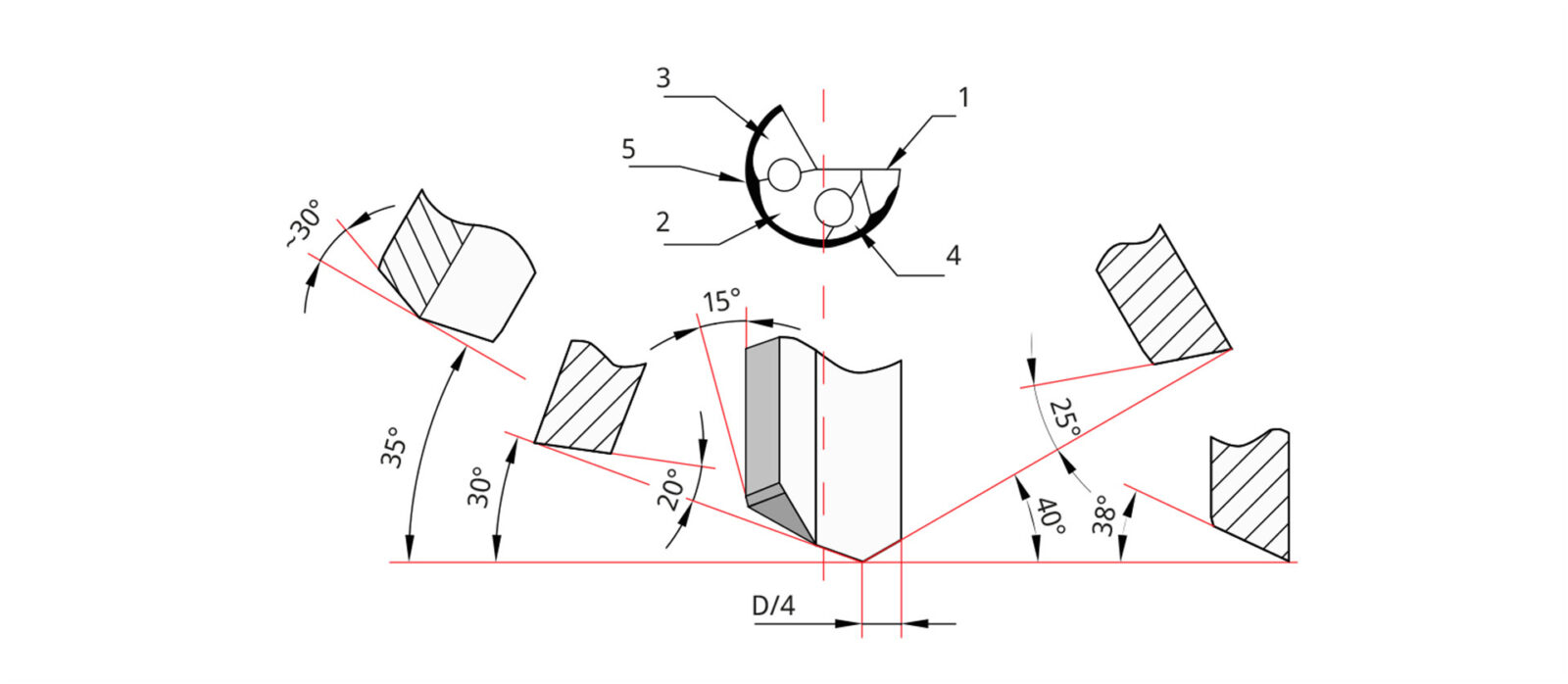
Standard grind section for single-lip drills with Ø = 5 to 30 mm
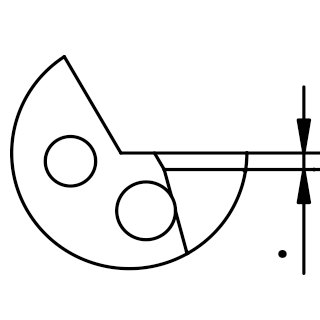
Step 1*
Axis A: -30°
Axis B: +12°
Axis C: +5°
Meas.: > D/4
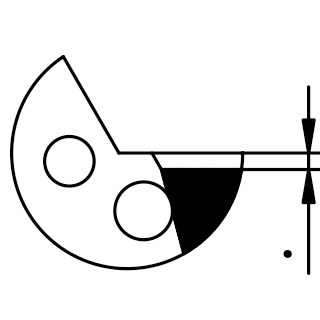
Step 2*
Axis A: 30°
Axis B: +20°
Axis C: +6,5°
Meas: 0,3…0,5
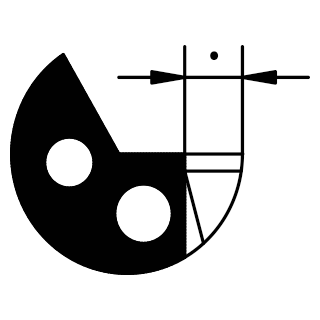
Step 3
Axis A: +20°
Axis B: +12°
Axis C: -5°
Meas.: D/4
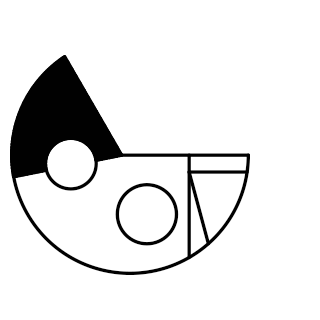
Step 4
Axis A: 30°
Axis B: +12°
Axis C: +55°
Meas.: —
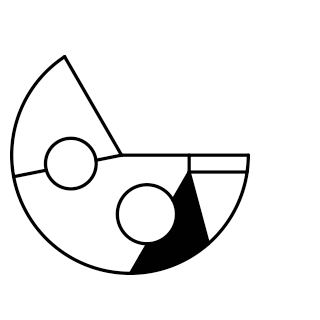
Step 5
Axis A: 0°
Axis B: +25°
Axis C: -5°
Meas.: —
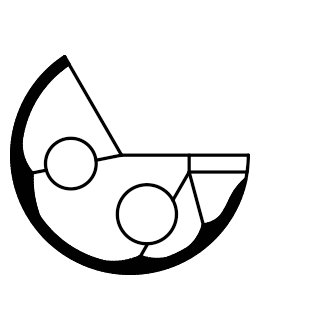
Step 6
Twist the single-lip drill lightly around the circumference without damaging the guide chamfer.
(*) Set Axis C such that the chamfer during the second pass is parallel to the chip face. The width of the chamfer is the same as that of the circular grinding chamfer.
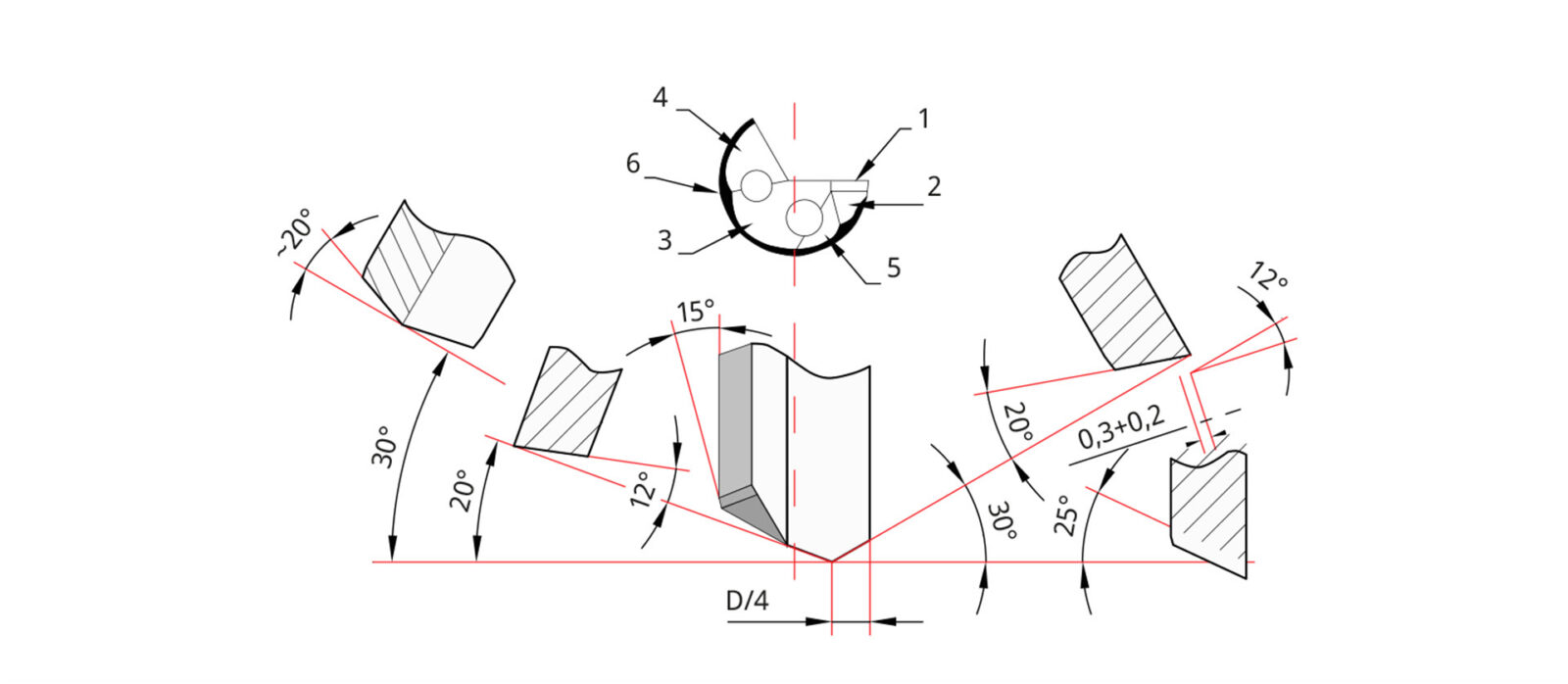
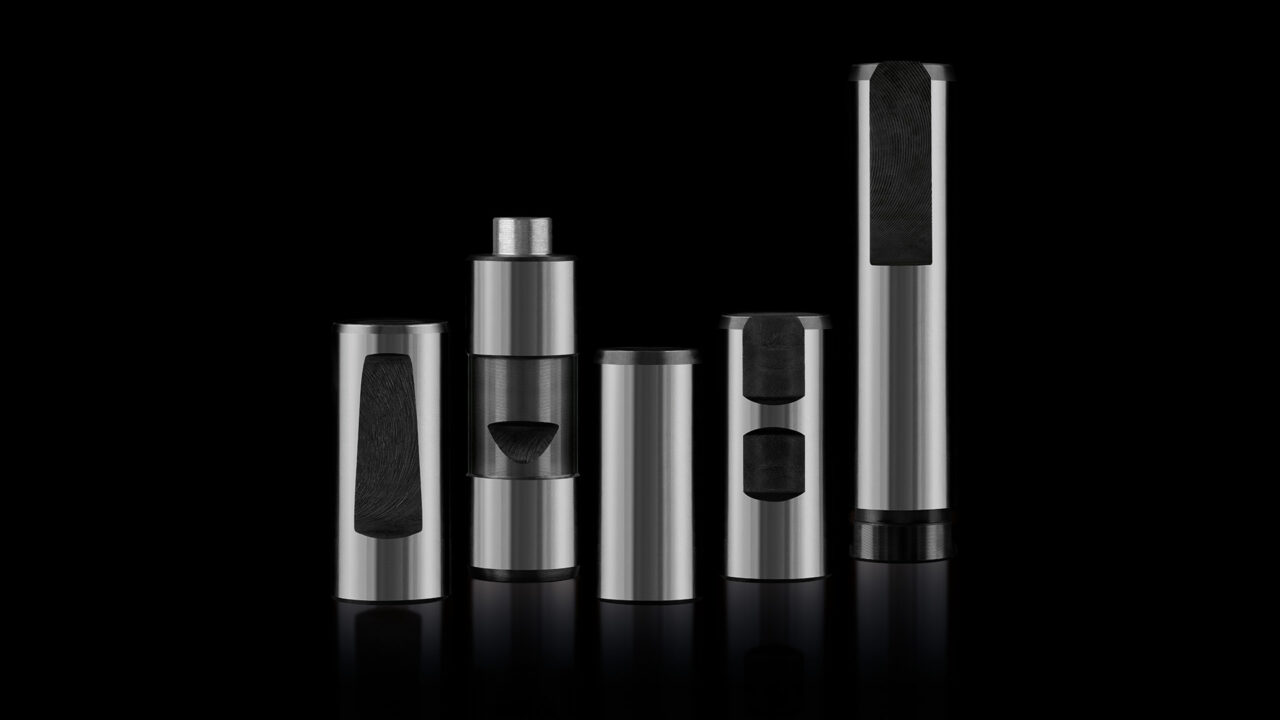
Clamping sleeves
Silmax can develop customised solutions based on a drawing or a sample supplied by customers.
Range of standard clamping sleeves
DM
IFE
IFA
IPFE
VDI
6535 HA
1835 E
6535 HE
6535 HB
6535 HB
Range of clamping sleeves for solid carbide drills
6535 PHA
6535 PHB
6535 PHE
1835 PFE
5320 TBN
Standard contour shapes
First choice for drills with long drill head and optimised contour geometry for drilling under difficult conditions, such as intersections and situations where cooling lubricant is insufficient.
Special geometry specifically studied for drilling when high precision and high-quality surface finish are required. Available on request.
Standard geometry suitable for drilling most materials.
Specific geometry studied for soft materials, such as for example grey cast iron, graphite, etc. used when it is necessary to maintain reduced drilling tolerances. Available on request.